Metal Matrix Composites (MMC): finally reaching the top of wish lists
Feb 27, 2018
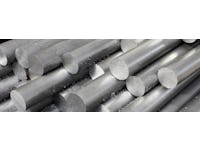
Metal Matrix Composites (MMC): finally reaching the top of manufacturers wish lists
Metal Matrix Composites (MMCs) have been known and explored for a very long time, but new innovations and an increased demand for high-performance lightweight materials means that they are finally ready to make it beyond their previous false starts.
There is a strong market pull for lightweighting, and to achieve this the most common metals employed are aluminium, magnesium, and titanium. Aluminium and titanium composites will be the focus in this article, but it is important for the reader to also note the emerging role additives can play in other metals such as copper for beneficial electrical and mechanical properties.
The additives can be split into nanotubes & 2D materials, particles, discontinuous fibres or whiskers, fibre monofilaments, and fibre tows. The key innovations, technical challenges, and early applications will be discussed below. For more detailed information on this plus market forecasts and company profiles based on extensive primary research see the IDTechEx report Lightweight Metals 2018-2028: Forecasts, Developments, Players.
The overriding challenges remain how the additives interact both with themselves (agglomeration and interfilament contact) and the matrix (wettability and unwanted reactivity). There is also the constant consideration of the pay-off between the beneficial properties and the higher price-tag, but this could finally be falling in favour of the MMCs.
Particles: Small is mighty
The use of ceramic particles, predominantly SiC, Al2O3, and AlN, have the largest market share of this industry. The advantages typically include improved strength, stiffness, corrosion resistance, and wear resistance as well as reduced thermal conductivity and thermal expansion. The improved strength and stiffness are particularly notable and relevant at elevated temperatures.
The problems have traditionally been that a high-percentage of volume inclusion is required for the beneficial properties and that brings manufacturing challenges, higher costs, and additional problems such as the inability to use conventional instruments in machining.
Materion AMC is one of the market leaders in this field with their SupremEX product range, they use a powder metallurgy process and SiC particles within the range of 17-40 vol%. For the 25% volume composition, the tensile modulus is 60% higher than the parent alloy (115 GPa). In 2015, their first material received AMS specifications and currently, small amounts are used in satellites, commercial and military aerospace, and in the low volume high-performance automotive market.
A notable new entry to this field are Gamma Alloys, they incorporate alumina nanoparticles into the matrix by using an aluminium particle as a carrier to prevent agglomeration. Although higher density than SiC and with worse properties, as reported by their competitors, alumina is chosen as it is cheaper (assisted by the high-demand from the cosmetic and semiconductor industry) and it is more machinable.
Gamma Alloys stated the size to be very important, the alumina nanoparticles (10-50 nm range) act as artificial precipitates and hinder the plastic flow. These nanoparticles remain at elevated temperatures and therefore one of the main advantages is a high strength at these temperatures when compared with commercial alloys. IDTechEx were told that the tensile strength of 100 MPa at 400 °C is achievable. Materion AMC uses SiC which are in the range of 2-3 μm but told IDTechEx they are experimenting using finer grades down to 0.3 μm. In November 2017, Gamma Alloys announced a recent investment from Boeing HorizonX, another indicator of the re-emerging interest in this field.
These are not the only significant developments in this field. More details on both companies mentioned and more can be found in the market report.
In addition, the reader should note that the use of beryllium metal in high percentage volumes as somewhat comparable technology. The key players and innovations in this work was highlighted in a previous article.
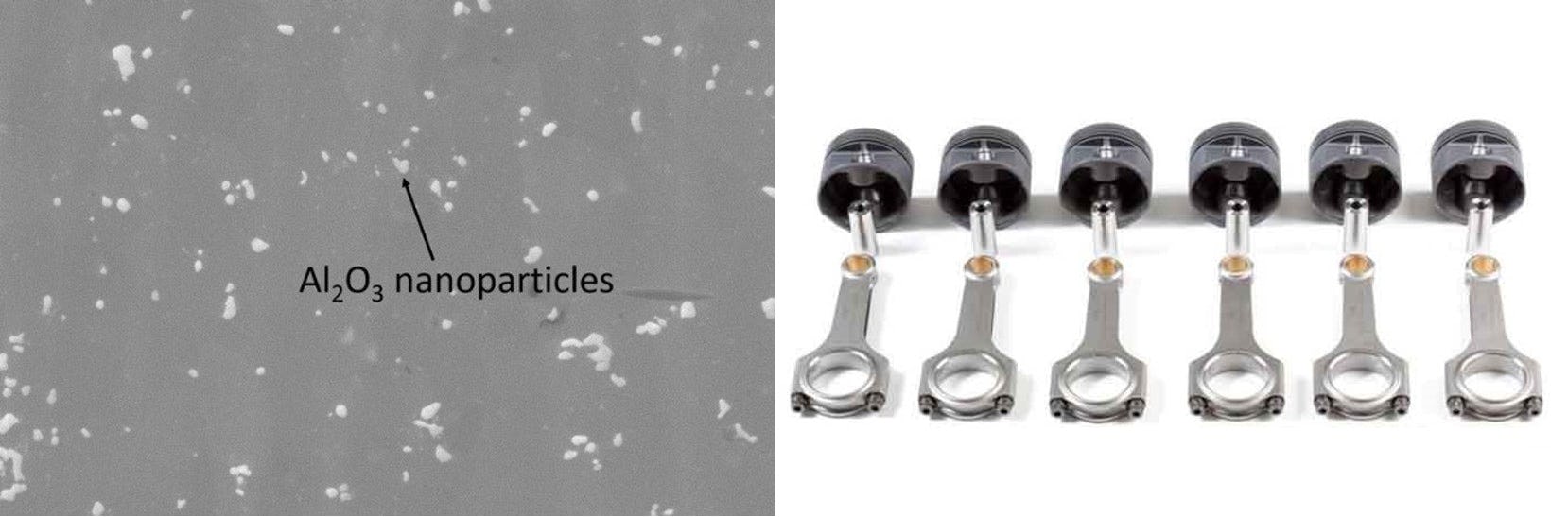
Microscope view of MMC from Gamma Alloys with the artificial precipitates indicated and an example of the MMC use in pistons. Source: Gamma Alloys.
Fibres: Not just for polymer substrates
As was seen in a previous article, continuous ceramic fibres are set to have a significant market growth as a result of their lightweight high-temperature potential in ceramic matrix composites (CMCs). This boom will allow a follow-on opportunity for the corresponding fibre use in metals, the start of this is already being observed and Alvant (previously CMT) are proving to be one of the early frontrunners. Alvant use continuous alumina fibre, branded Nextel, from 3M with an aluminium matrix. This can be used for complete parts or as inserts which are then overmolded by aluminium. The work with Jaguar Land Rover was introduced in the previous article, and recent project announcements with Yasa Motors and GE Aviation for computational design and analysis and M Wright & Sons for the use of woven ceramic fibres, give an indication of the potential significant applications and ongoing research areas.
Ceramic fibres are not the only opportunity, there are also monofilaments and whisker additives that have some market potential and emerging players. The exact property benefits from the additional cost have still yet to be fully established. Below are two additional images: The central image is of monofilament reinforced titanium hydraulic actuator pistons, which are 40% lighter than steel and corrosion resistance developed by TISICS, they told IDTechEx they are currently developing a towpreg variant for improved part manufacturing. The right-hand side image is of some aluminium bearing liners reinforced with short alumina fibres from FRA Composites. The mechanical improvements and wear resistance of this material has resulted in it being linked with all the main helicopter manufacturers.
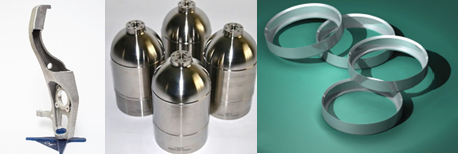
From left to right: suspension upright from Alvant, hydraulic actuator pistons from TISICS, and aluminium bearing liners from FRA Composites. Source: Alvant, TISICS, FRA Composites
Nanotubes & 2D materials: Carbon isn't the only option
Carbon Nanotubes and graphene have been speculated for a wide variety of applications and this field is no exception to that trend. The challenges faced here are not only the usual agglomeration prevention and raw material consistency, but also unfavourable reaction with molten aluminium metal. These problems and a lack of overwhelming property advantages have resulted in this field not being aggressively pursued, but the reader should note that this is not the case for copper which has a wealth of ongoing research and interest.
Boron Nitride Nanotubes (BNNTs) on the other hand have demonstrated more promise. BNNTs do not interact with the molten metal substrate in the same way and the high-temperature stability and resultant applications lend itself nicely to advanced lightweighting. NASA has highlighted the potential use for BNNTs up to 850 °C and it has been proposed for potential use within a supersonic plane. Serval other research institutes have also targeted this area, with World Premier International (WPI) Center for Materials Nanoarchitectonics developing a BNNT reinforced aluminium ribbon and Deakin University making 3D printed BNNT titanium composites.
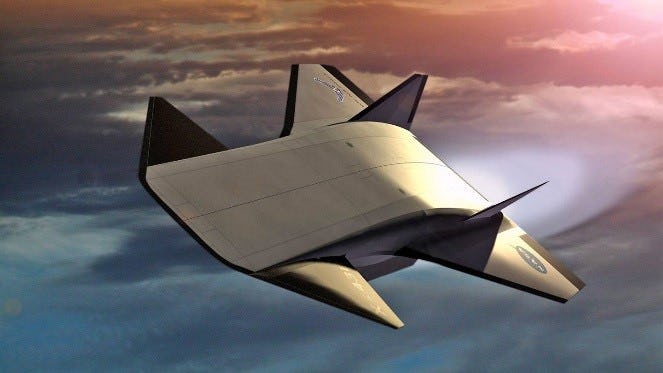
Illustration of the NASA X-43B hypersonic flight vehicle. Source: NASA
For more information on all of this analysis into the advancements of MMCs including company profiles, granular 10-year forecasts, cost progressions and more about aluminium, magnesium, and metal foams then see the report from IDTechEx: Lightweight Metals 2018-2028: Forecasts, Developments, Players.